Australia's miners and unmanned aerial vehicle operators are increasingly reliant on locally built drones for trials and implementations.
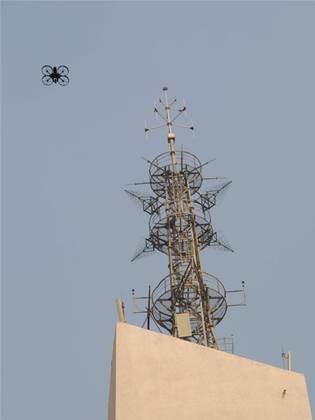
Perth firms A.I. Tech and Cyber Technology are among the new breed of UAV manufacturers and integrators to offer locally-built aircraft for sale and rental.
Australian companies have traditionally used craft built overseas, with US manufacturer Rotomotion a popular early choice. However, they are less favoured now than they were several years ago, as companies increasingly look to avoid the hassle of gaining US export clearances.
Read part one of iTnews' investigation into how Australian companies use UAVs.
Although HELImetrex operates a Rotomotion, CEO Ray Gillinder says the company will soon be "disbanding" it.
"Too long a setup time and too many moving parts essentially," he says.
Adam Technology has also stopped using Rotomotions. "Our pilots that we used to use to fly [Rotomotions] for us have actually set up their own company, and are manufacturing their own UAVs, which are a lot better," managing director Jason Birch says.
The US is trying to hasten export clearance of UAVs for foreign buyers as it faces a "record" $327 billion backlog of arms exports.
Although the action comes too late for some operators, it hasn't dissuaded all from buying UAVs made offshore.
HELImetrex, for example, has bought a German-produced Microdrones UAV, which is currently "on its way" to Australia.
However, Adam Technology is using an MX-880 vertical take-off and landing (VTOL) aircraft produced by under-the-radar Perth firm A.I. Tech.
"It's the same basic idea as the Rotomotion ones," Birch says. "They're what they call a 90 size helicopter with an autonomous flight controller attached."
Serious business
Like many other UAV makers, A.I. Tech keeps most of its technical specifications under wraps. The company does not even maintain a web presence.
A.I. Tech director Kevin Lunn tells iTnews that the firm manufactures its craft "to do a job, not to sell on to other people.
"All the UAVs you buy off the shelf are built to a price," he says, warning the propensity of some players to use components more suited to hobby craft.
"Don't get me wrong here - we use an airframe that is from the hobby industry.
"We have to because it makes sense. There's no point in us spending $12 million on machines to manufacture an airframe that we can actually modify to our own technical specifications.
"But its the rest of the things inside the aircraft - the power systems, the dual downlinks and uplinks that we use. It's all these things that make our UAV very different from the basic UAV out there."
Lunn says A.I. Tech is "now starting to test fly multi-bladed rotor systems" capable of carrying a payload of up to ten kilograms.
"Although we do have multi-rotor platforms that we can use, we don't want to because they just don't have the runtime, the lifting capacity. They don't have so many things," he says.
"We find that what we have in our particular MX-880 is ... a lot of potential to do a lot of things with it without having to change the platform. We can fly faster, higher, there's a lot of things we could do."
However, Lunn says he and fellow director Nigel Brown have no problem building a UAV to meet a desired specification.
"Be it fixed-wing, rotary-wing or multi-rotor, it doesn't really matter which platform we need to utilise; it just depends on the job we've got at hand," Lunn says.
Fellow Perth manufacturer Cyber Technology offers fixed-wing and quad-rotor UAVs, though its CyberQuad Maxi is most commonly used for civil applications, such as on mine sites.
Rival manufacturer UAVs Australia, meanwhile, is importing an unknown quantity of fixed-wing UAVs into Australia.
"We have a relationship with a manufacturer of a mature platform and we've just purchased those systems from them, and we're integrating them here in Australia with a gimbal, autopilot and transponder technology and all the things they need to be able to operate comprehensively in Australian airspace," commercial director Mark Stevens says.
"We've sourced all those parts individually and we're integrating them here in Australia, and then we're taking them onsite.
"We've got a series of nodes we've set up around Australia in the key areas where our clients are operating, and we're operating from there. At the moment they're all remote locations."
Some models were not raised by those iTnews interviewed but are known to be possible for civil applications, such as the Yamaha RMAX, Leptron's VTOLs and Lehmann Aviation fixed-wings.
Read on to the next page for UAV designs - VTOL vs fixed-wing.
There are advantages and disadvantages of each type of craft, but essentially they can be boiled down to flight efficiency, image accuracy, take-off and landing, and payload capability.
While fixed-wing UAVs are generally noted for their flight efficiency for aerial mapping applications, they may face challenges operating in smaller, more confined areas on mine sites.
"I believe the fixed-wings have gotten some traction because fixed-wings do cover a large amount of area more cost efficiently," Cyber Technology project manager Joshua Portlock says.
"However, they are also a bit limited in their operation and flexibility when doing closer range, higher resolution work."
VTOL UAV operators frequently cite image overlap and overshoot as key areas where their craft excel over fixed-wing UAVs.
For aerial mapping or stockpile surveys, several passes over a site may be required to build up an accurate image of the survey area.
The UAV's ability to turn around at the end of each pass impacts its flight efficiency.
"To do say 25 hectares [a 500m x 500m area], [fixed-wing UAVs] would have to overshoot - so they'd fly over that 500 metres then they'd overshoot... to do a big arc and turn around and come back again," Portlock says.
"It's inefficient use of flight time to cover that relatively small area.
"A VTOL can pop up and position itself accurately within that half kilometre square to [go] back and forth quite time-effectively."
Crosswinds may also impact the number of passes required to complete a site survey. Fixed-wing UAVs may require more passes to counter the effect of crosswinds on image capture, says Adam Technology's Jason Birch.
"If there's crosswinds then the images all have a skew to them unless you have a more sophisticated camera that allows you to compensate for that," Birch says.
"Because of the degree of sideways angle in the images, [fixed-wing UAVs] tend to fly very high overlaps which means you get a lot more photos for the same area.
"Even though they're flying faster and able to fly for longer [than VTOL UAVs], they don't actually get more coverage in the end because they're soaking it up with the extra overlaps to try and make sure there's no gaps between the images."
VTOL operators also see take-off and landing as a key area of ascendancy over fixed-wing craft.
Most fixed-wing UAVs require a landing strip for both take-off and land. The Gatewing X100 used by the Australian arm of Belgian mine giant Sibelco is slightly different, in that it uses a catapult launcher for take-off. However, it still requires a flat surface to belly land.
The makers advise "an 'airstrip' without obstacles measuring 30m wide and 150m long".
"The X100 lands typically within a 15m radius but due to barometric errors a 150m long airstrip is advised to be sure of a safe touch down," the company states.
Although this did not appear to be a hindrance to Sibelco, HELImetrex chief executive Ray Gillinder sees it as a disadvantage in the confines of a mine environment.
"What people fail to realise is on mine sites there's a lot of OH&S scenarios in place," Gillinder says.
"In certain mine sites [where] you've got a set of stockpiles or washer plant, you're working in a fairly confined area. There's sometimes not a lot of opportunity to put the aircraft down within close quarters."
Gillinder questions the long-term impact of landing a UAV on its fuselage, particularly on an unprepared landing strip.
"Mine sites are typically very rugged terrain, and a lot of bare earth," he says.
A YouTube video from Spain shows the wheel-less Gatewing X100 belly-land on flat, albeit rough, terrain. The undercarriage is not visible.
iTnews contacted the Australian distributor of the X100, Pitcher Partners, for comment, but a representative was unavailable at time of publication.
"We find that the availability of take off and landing [with VTOL] allows us to work a lot tighter, a lot closer [to mine infrastructure]," Gillinder says.
Portlock concurs: "You can take off from a compact area. You don't need to have a launching mechanism and a recovery area, so even if it's quite obstructed environment, you can still VTOL out of the small area you've got to work from".
Close-working is also a current regulatory requirement. The Civil Aviation and Safety Authority (CASA) only allows UAVs to be operated in visual meteorological conditions - i.e. within sight - and to a height of 400ft (121m) if special approvals aren't sought (pdf).
"Visual range is only about one kilometre at most," Birch says. "As soon as you get past a kilometre away you really can't see them.
"That limits how big your [flying] footprint is on a single flight anyway, which negates a fair bit of the advantage of a fixed-wing."
This article is part of a special investigation into the use of UAVs in Australian mines. Stay tuned to iTnews tomorrow for the next installment.