Australia's miners will soon be taking advantage of sophisticated physics engines found in computer games to improve the accuracy of explosives used to blast ore from the ground.
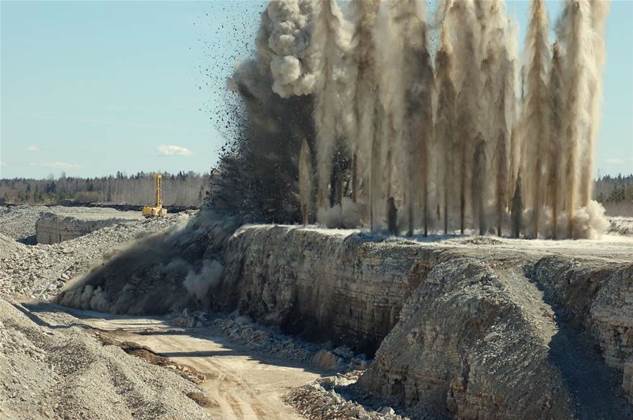
Today iTnews studies the rise of technology systems that underpin rock blasting in open pit and underground mine operations, such as predictive modelling, radio-controlled detonation, real-time monitoring and post-blast data analysis.
Across the blast lifecycle, IT systems are used to record, manage and analyse data being generated.
Poor blasting execution not only has negative economic consequences, but is also a safety and environmental hazard, with ground vibration, airblast overpressure, dust, fumes, and the potential for flyrock all important considerations for miners.
Blast engineers are ideally trying to predict three outcomes in blast design: fragmentation (the size distribution of the blasted material), movement (where the grade and waste will end up), and environmental consequences, according to W.H. Bryan Mining and Geology Research Centre (BRC) principal mining engineer Alan Cocker.
Cocker told iTnews that although three-dimensional blast movement models have been in development "over a number of years, [they] have never achieved their potential for site use".
However, he believed that could change via joint research works between BRC and the federal government's CRC ORE cooperative research centre.
"With the massive increases in computer power over recent years and the advent of the sophisticated physics engines used in the computer games industry, a workable three dimensional movement model that uses crucial elements of real physics is in reach," he said.
Open source physics engines such as Bullet, which have previously been used for 3D collision detection and soft body/rigid body dynamics within video games (Grand Theft Auto IV, Red Dead Redemption) and video effects in movies (Shrek 4, Sherlock Holmes), are now being adapted to the resources industry.
"Clearly, there is a difference between Joe Blow fragging and nuking aliens one by one and 130,000 uniform blocks in motion, each colliding with one another," Cocker said.
"What we hope to offer the mining industry is a modelling tool that can predict ore movement to minimise the twin evils of loss and dilution. You need to know where the good stuff ends up after the blast, or you’ll be processing waste and dumping ore! In a perfect world ore would be green and waste red (or black). Unfortunately they can look identical, and dig lines are often laid out as though the stuff hasn’t moved at all."
Blast design
Predictive blast fragmentation models used in the past have typically been either numerical or empirical, Cocker said.
Numerical models such as discrete element method (DEM), he noted, are onerous to configure and demanding of resources — both computing and human — and are generally not appropriate for operational use at mines.
"The problem with empirical models, by contrast, is that they tend to operate at a scale too coarse to give results useful for optimisations," he added, noting typical Kuz-Ram-based fragmentation models [pdf] (widely used to estimate fragmentation from blasting) assume homogeneous geology (the same type of materials) throughout a blast.
CRC ORE's integrated blasting software, SMI BlastOre, is being developed to provide modelling support for existing blast design editors, such as JKSimBlast, incorporating a 3D blast movement model based on a physics engine.
"In many ways SMI BlastORE is just a further step on the path towards a complete blast design and modelling package; it does not design blasts itself, but instead supports the blast design editor by providing an advanced predictive modelling toolkit," Cocker said.
"What is needed ultimately is a fully featured and integrated blast design (IBD) package with a plugin interface to support current and future predictive blast performance models; the IBD should be fully 3D and fully responsive to geological and geotechnical variation."
Cocker noted mining companies are ultimately seeking ease of use and integration.
"What they really want is a big 'GO' button in their chosen mine planning software to instantly access and model all the available data, pasting the best possible blast design back into the host software," he said.
"As part of this process an ideal IBD would also supply field equipment, such as autonomous drills and smart explosives trucks, with the required menus in order to implement the ideal design automatically."
Read on for how miners are using radio networks and video for blast accuracy...
Advanced detonation
Further into the blast lifecycle, Ian Gipps, CSIRO stream leader for non-entry underground mining, told iTnews that advanced methods of detonation have the potential to deliver greatly improved blasting accuracy.
"Currently all the detonators are connected up, mainly by electrical wiring," Gipps observed.
"Particularly underground, when you've got a large pattern where you might have ... up to 1000 holes, making sure you connect all the wires in the correct order can be a little difficult.
"With the electronic dets [detonators] it is not quite so critical.
"One of the other major areas where IT has come in, particularly in underground blasting, [is] through-rock radio communications to the blast and detonation circuit to set the detonation off, so that you can move away ... and [conduct the blast from] safer areas."
Gipps said radio detonators are another step towards mine site automation.
"One of the areas that will be much more important from the IT point of view will be the automation of explosive loading and explosive detonation; for further advanced blast control we need to go into automation of the explosive loading," he said.
Indeed, Rio Tinto announced last year it is trialling autonomous production drills designed to provide a reliable and repeatable process in blast-hole drilling.
The iron ore giant will use the integrated system to allow automated blast-hole drill rigs to precisely position the blast holes, conduct live rock analysis, dictate to the explosives delivery vehicle the correct explosive charge for each hole, and provide data supporting 3D mapping systems to provide detailed imaging of each deposit.
After the blast
As part of the blast lifecycle, miners are additionally undertaking ongoing analysis derived from routine monitoring.
Monitoring systems, conveying a variety of data via 3G, radio, or satellite links, process information in real-time.
BHP's Mt Arthur Blast Monitoring Program has six dedicated monitoring units permanently installed at specific locations throughout the coal mine's NSW Upper Hunter Valley site, feeding back into an automated web-based system, providing real-time vibration and overpressure data.
Rio Tinto subsidiary Coal & Allied's Mount Thorley Warkworth network, also situated in the Hunter Valley, consists of five real-time dust samplers, transmitting back to a central database, sending an alarm (on the basis of a rolling three hour average) to environmental personnel when particulate matter levels reach trigger levels at neighbouring residences.
Explosive video
Cocker additionally noted, as part of the post-blast monitoring process, most miners are now filming open-cut blasts, utilising modern video technology, providing high-definition, high-speed (ultra-slow motion) capabilities.
With consumer cameras capable of up to 300 frames per second also in use, there is now little reason for miners not to film in both high definition and at high speed.
"These [images] have the potential for quantitative assessment," he commented.
"Where permitted, markers, such as cuttings cones, can be suspended over the face; these are then picked up by the surveyors, together with camera locations.
"It will then be possible to calculate first burden movement times and face velocity profiles, as the marker movements are tracked by the video camera(s)."
Cocker noted modern video is an encompassing blast recording device, while a video archive can shed light on a pit's 'blastability', fuming and dust generation propensity.
"They are ideal for a quick qualitative overview of many key blast performance indicators," he commented.
"Timing accuracy, face profiles, flyrock and fuming timing and origins, and the final muckpile shape; if the video records are archived, they can be used to identify consistent blasting problems in particular areas of the pit."